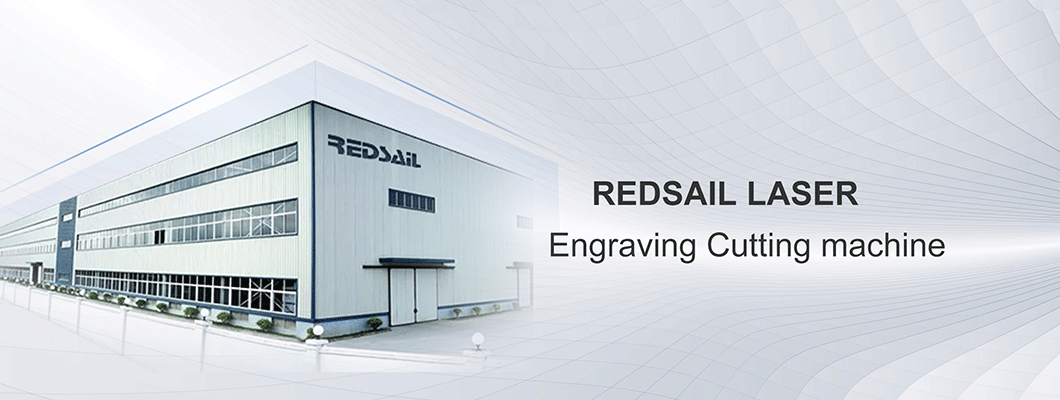
At present, the demand for high-power laser cutting machines is increasing, mainly focusing on the cutting of thick plates. However, thick plate cutting has high requirements for laser cutting machines. Whether it is cutting speed or cutting cross-section, it is a test of the technology of laser cutting machine manufacturers. What problems will be encountered in cutting thick plates?
Next, let's analyze the beam laser for everyone.
Thick plate perforation
Laser perforation is the first action before cutting, and the thicker the plate, the longer the perforation time. Therefore, in order to improve cutting efficiency, many laser cutting machine manufacturers will improve the perforation time. Then, when piercing, the more common problem is hole bursting. The reason for this problem is the high power piercing, which is fast: the huge energy injected during the piercing increases the temperature of the plate and then affects all subsequent cutting. When using low-power pulse for piercing, the cutting power will be reduced and the Unit cost will be increased for a long time.
Cutting section
The difficulty of laser cutting thick plates is much higher than that of thin plates, and the aesthetic appearance of the cutting section is more obvious than that of thin plates, with poor accuracy. Even serious slag sticking and other phenomena may occur, making the processing value of laser cutting machines not fully reflected.
Leave a Comment