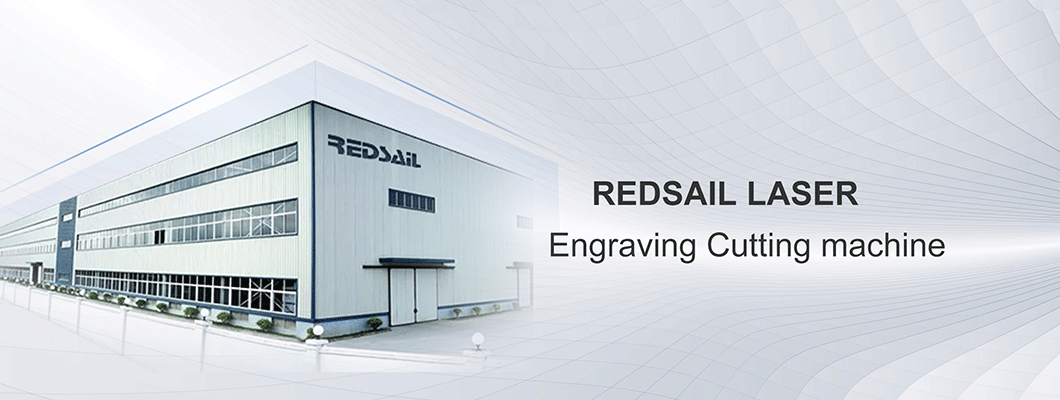
Laser cutting refers to focusing the laser light emitted from the laser into a high power density laser beam through an optical path system. The laser beam irradiates the surface of the workpiece, causing the workpiece to reach a melting or boiling point, while the high-pressure gas coaxial with the beam blows away the molten or vaporized metal. As the light beam moves relative to the workpiece, the material eventually forms a cutting seam, thereby achieving the purpose of cutting. Laser cutting is one of the thermal cutting methods. There are four main types of laser cutting methods to cope with different situations. Below is a detailed answer from Redsail Laser.
1、 Melt cutting
When the power density of the incident laser beam exceeds a certain value, the interior of the material at the beam irradiation point begins to evaporate, forming holes. Once this small hole is formed, it will act as a black body to absorb all the energy of the incident light beam. The small hole is surrounded by a molten metal wall, and then an auxiliary airflow coaxial with the light beam carries away the molten material around the hole. As the workpiece moves, the small holes move horizontally and synchronously in the cutting direction to form a cutting seam. The laser beam continues to irradiate along the front edge of this slit, and the molten material is continuously or pulsatively blown away from within the slit.
2、 Vaporization cutting
In the process of laser vaporization cutting, a high-energy and high-density laser beam is used to heat the workpiece, raising the temperature, and vaporizing the material into steam in a short time. When the steam is emitted, a notch is formed on the material, thus achieving the cutting effect. However, the heat of vaporization of general materials is high, so the speed at which the surface temperature of the material rises to the boiling point temperature is fast enough to avoid melting caused by heat conduction. During vaporization and cutting, the steam carries away molten particles and washes away debris, forming holes. During the vaporization process, about 40% of the material is vaporized and disappears, while 60% of the material is expelled by the gas flow in the form of molten droplets. In this case, very high laser power is required. To prevent material vapor from condensing onto the slit wall, the thickness of the material must not significantly exceed the diameter of the laser beam. This process is therefore only suitable for applications where the exclusion of molten materials must be avoided.
3、 Controlled fracture cutting
For brittle materials that are prone to thermal damage, high-speed and controllable cutting through laser beam heating is called controlled fracture cutting. The main content of this cutting process is: the laser beam heats a small area of brittle material, causing large thermal gradients and severe mechanical deformation in the area, causing cracks to form in the material. As long as a uniform heating gradient is maintained, the laser beam can guide cracks to develop in any desired direction. The materials commonly used in this type of cutting are brittle materials such as glass cutting. Note that this controlled fracture cutting is not suitable for cutting sharp corners and corner cut seams. Cutting oversized closed profiles is also not easy to achieve success. The control of fracture cutting speed is fast and does not require too high power, otherwise it will cause the workpiece surface to melt and damage the cutting edge. The main control parameters are laser power and spot size.
4、 Oxidation melting cutting
Inert gas is generally used for melting and cutting. If oxygen or other active gases are replaced, the material is ignited under the irradiation of a laser beam and undergoes a fierce chemical reaction with oxygen to generate another heat source, which further heats the material. This is called oxidative melting and cutting.
There are two heat sources in the oxidation melting cutting process - laser irradiation energy and thermal energy generated by the chemical reaction between oxygen and metal. In the oxidation melting cutting process with two heat sources, if the combustion speed of oxygen is higher than the moving speed of the laser beam, the cutting gap appears wide and rough. If the laser beam moves faster than the combustion speed of oxygen, the resulting slit is narrow and smooth. Melt cutting can save a lot of energy compared to vaporization cutting, and is commonly used for some metals that are not easily oxidized, such as stainless steel, titanium, aluminum, and their alloys.
Leave a Comment