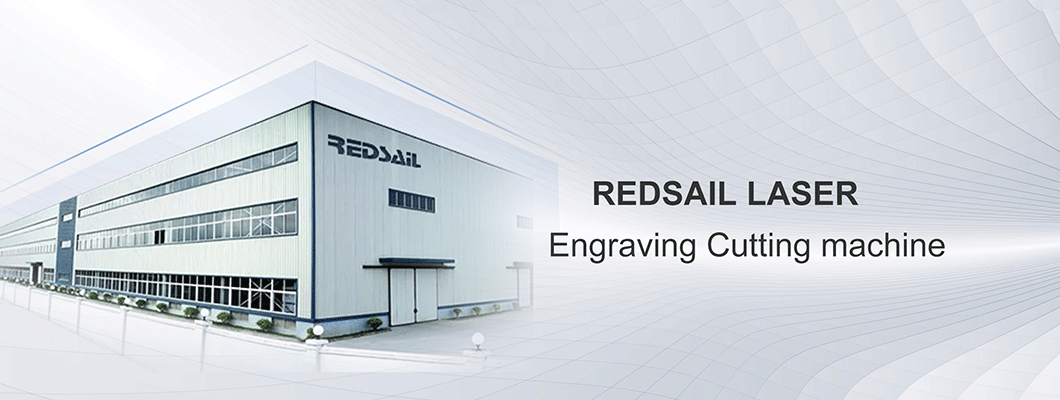
Generally suitable for cutting carbon steel and other workpieces below 5mm, the focus of the cutting machine is close to the surface of the workpiece. The smoothness of the upper and lower surfaces of the workpiece varies in this mode. Generally speaking, the cutting surface near the focus is smoother, while the lower surface far from the cutting focus is rougher. This mode should be determined based on the process requirements of the upper and lower surfaces in practical applications.
2、 Positive focal length: the focal point of the workpiece surface
When the workpiece you need to cut is stainless steel or aluminum steel plate, you often use the pattern of cutting points in the workpiece. However, one drawback of this method is that due to the focus principle, the cutting amplitude of the cutting surface is greater than the cutting point on the workpiece surface. At the same time, this mode requires a large cutting airflow, sufficient temperature, and slightly longer cutting and perforation time. Therefore, when the workpiece material you choose is mainly stainless steel or aluminum with high hardness.
3、 Negative focal length: focal point on the surface of the workpiece
Because the cutting point is not located on the surface or inside of the cutting material, but above the cutting material. This method is mainly used for cutting materials with high thickness. The reason why this method focuses on cutting materials is mainly because thick plates require a larger cutting range, otherwise the oxygen conveyed by the nozzle can easily cause a decrease in cutting temperature. But one drawback of this method is that the cutting surface is rough and not very suitable for high-precision cutting. Maintaining a reasonable and constant relative position between the laser focus and the processing object has become a key technology in laser cutting.
The automatic tracking system can be considered from two aspects:
(1) How can the relative position between the laser focus and the processing object be detected stably, reliably, and conveniently?
Laser processing belongs to non-contact processing and cannot directly detect the focus position. The focus position is determined by the distance between the focusing mirror and the surface of the processed object. Therefore, the commonly used method is to detect the distance between the focusing mirror and the surface of the processed object, thereby indirectly detecting the relative position of the laser focus and the surface of the processed object.
(2) How to quickly compensate for the design problem of the position servo system after detecting changes in the laser focus and the position of the processing object
Using a microcontroller minimum system to control a stepper motor to achieve a typical separation focus tracking system. Due to the simple performance of the microcontroller, it is difficult to implement more complex control strategies, while the dynamic characteristics of ordinary stepper motors are poor, making it difficult to meet the fast requirements of laser focus tracking. In order to overcome the above shortcomings, the laser focus automatic tracking system based on the motion controller uses the optical code disk as the displacement sensor, and uses the main tracking (electronic gear) function of the motion controller to quickly compensate the focus position error.
Leave a Comment