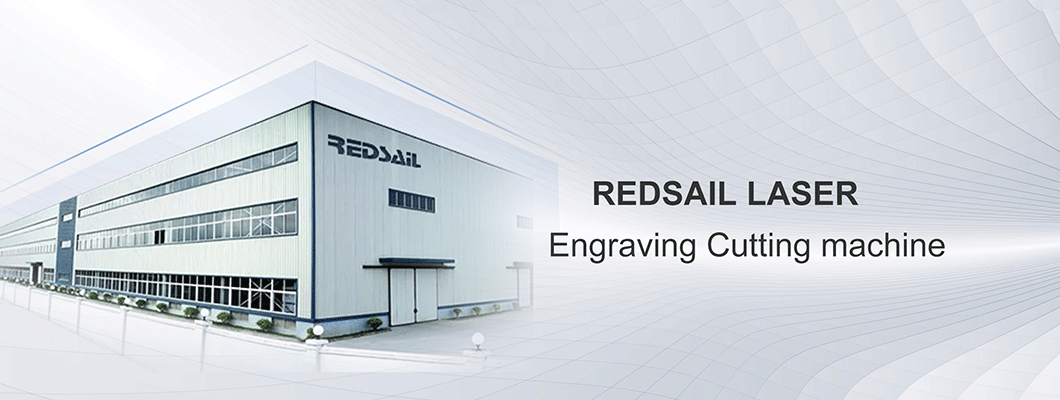
Burrs refer to irregular metal parts such as various sharp corners and burrs that appear at the transition of the workpiece surface during laser cutting. Burr is one of the common phenomena in laser cutting machining, and it is also the two major problems "burr generation and control" that have not been solved so far in the theoretical research of metal cutting. Burrs directly affect the dimensional accuracy, shape and position accuracy and surface roughness of the workpiece to be processed.
1. Reasons for burrs in sheet metal processing by laser cutting machine:
The main reason for burrs in sheet metal processing by laser cutting machine: When the laser cutting machine is processing the workpiece, the high energy generated by the laser beam irradiating the surface of the workpiece makes the surface of the workpiece vaporize quickly and evaporate to achieve the purpose of cutting. Tihao Machinery is the company's main products with rotary top, screw, shaft machining, CNC lathe machining, tool holder and chuck adapter, but there is a core device here that we must pay attention to, that is, auxiliary gas. The auxiliary gas is to blow off the slag on the surface of the workpiece after the irradiated surface of the workpiece is vaporized. If the auxiliary gas is not used, after the slag cools, a burr will be formed and attached to the cutting surface. This is the main reason for the formation of burrs.
Another reason is the quality of the equipment itself, as well as the parameter setting factor. After the customer purchases the laser cutting machine, a professional operator must debug the equipment.
Solutions for burrs in sheet metal processing by laser cutting machines:
1. Be sure to equip an air compressor and use auxiliary gas for cutting.
The purity of the gas should be high. You can change to a gas supplier with better quality. The purity of the gas is very important. It is best not to use cylinder gas, because after two fillings, the purity is not good, and the gas is wasted.
Such as laser cutting stainless steel, it is recommended to use nitrogen as the auxiliary gas. Nitrogen is a flame retardant gas. During laser processing, nitrogen not only prevents the explosion point phenomenon of laser cutting, but also the heated end face will not be instantly oxidized, and the cut end face will be smoother and brighter. The auxiliary gas should be adjusted to a pressure of 12-15 kg. The nitrogen under this pressure will not completely prevent the combustion, but also can quickly blow away the waste to achieve the effect of removing burrs.
2. Find a professional operator to debug the parameters of the metal laser cutting machine until it is normal, and the cutting operation of the metal laser cutting machine can be successfully completed.
Some parameter setting factors of the laser cutting machine will also affect the appearance of slag, which will lead to the burr of the metal laser cutting machine, so it is necessary to adjust the cutting parameters to the best, air pressure, flow, focal length, cutting speed, etc., after many times Adjustment, relying on the parameters provided by the machine cannot cut exquisite workpieces.
The laser cutting machine is a precise machine, and the operation is also a delicate work. Often a data error will cause its work to run abnormally. Therefore, it must be strict and precise in the work to reduce and avoid errors. Equipment + gas + parameters are adjusted to the best, and the cut workpiece is free of burrs, which makes the cutting of the laser cutting machine more high-quality.
Burrs only occur in metal cutting, and there is no burr problem in non-metal cutting. How does the glitch occur? In fact, burrs are excessive residue particles on the surface of metal materials. If a material has burrs, then the material can be qualitatively defective. The more burrs, the lower the quality.
2. According to the working principle of the laser cutting machine, the reasons and solutions for the burrs are analyzed and obtained:
1. The upper and lower positions of the focal point of the beam are deviated. Solution: Adjust the position of the focus according to the offset position it produces.
2. The output power of the machine is not enough. Solution: Check whether the laser cutting machine is working normally. If it is not normal, it needs to be repaired and maintained in time. If it is normal, check whether the output value is correct.
3. The wire cutting speed of the cutting machine is too slow. Solution: adjust and increase the wire cutting speed in time.
4. The purity of the auxiliary gas of the cutting machine is not enough. Solution: Explain increasing the purity of the auxiliary gas.
5. The addition point of the laser beam of the cutting machine is offset. Solution: Debug the focus and make adjustments in time.
6. The laser cutting machine is unstable due to the long operation time. Workaround: Power off the machine and let the machine rest.
The metal laser cutting machine is a precise machine, and the operation is also a delicate work. Often a data error will cause its work to run abnormally. Therefore, it must be strict and precise in the work to reduce and avoid errors.
Leave a Comment