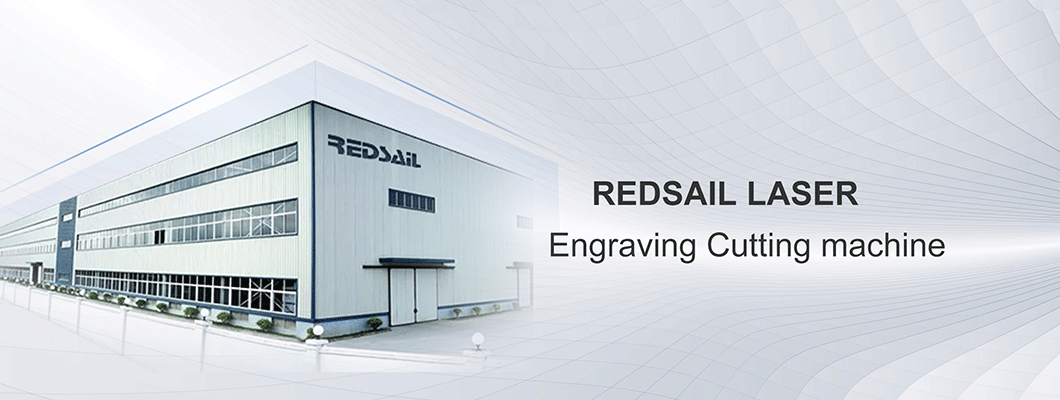
High power laser cutting machines have unparalleled advantages such as large cutting width, fast cutting speed, and the ability to cut thicker plates. High power laser cutting has gained unanimous recognition in the market. However, due to the fact that high-power cutting technology is still in its early stages of popularization, some operators are not very proficient in the skills of high-power laser cutting. Here are some difficulties and solutions in the cutting process of high-power laser cutting machines:
If the cutting effect is found to be poor, the following reasons should be investigated first:
1. All lenses inside the laser head are clean and free from contamination;
2. The water temperature in the water tank is normal, and there is no condensation on the laser;
3. The cutting gas has excellent purity, smooth gas path, and no gas leakage phenomenon.
Problem 1: Cutting with stripes
Possible reasons:
1. Incorrect nozzle selection, nozzle too large;
2. Incorrect air pressure setting, excessive air pressure setting resulting in burning and streaking;
3. The cutting speed is incorrect, and too slow or too fast cutting speed can also cause excessive burning.
terms of settlement:
1. Replace the nozzle, replace it with a smaller diameter nozzle, such as a 16mm carbon steel bright cut, and choose high-speed nozzle D1.4; 20mm carbon steel bright surface can choose high-speed nozzle D1.6;
2. Reduce cutting pressure and improve the quality of end face cutting;
3. Adjust the cutting speed to match the power and cutting speed appropriately.
Problem 2: There are nodules at the bottom
Possible reasons:
1. The nozzle selection is too small and the cutting focus does not match;
2. Air pressure too low or too high, cutting speed too fast;
3. The material of the board is poor, the quality of the board is not good, and it is difficult to remove lumps with small nozzles.
terms of settlement:
1. Replace the large-diameter nozzle and adjust the focal point to the appropriate position;
2. Increase or decrease the air pressure until the air flow rate is appropriate;
3. Choose good boards.
Problem 3: There are burrs at the bottom
Possible reasons:
1. The nozzle diameter is too small to meet the processing requirements;
2. Negative defocus mismatch, should increase negative defocus and modulate to appropriate position
3. The air pressure is too low, resulting in burrs at the bottom that cannot be fully cut.
terms of settlement:
1. Selecting a large-diameter nozzle can increase air flow rate;
2. Increase negative defocus to reach the bottom position of the cutting section;
3. Increasing air pressure can reduce bottom burrs.
Leave a Comment