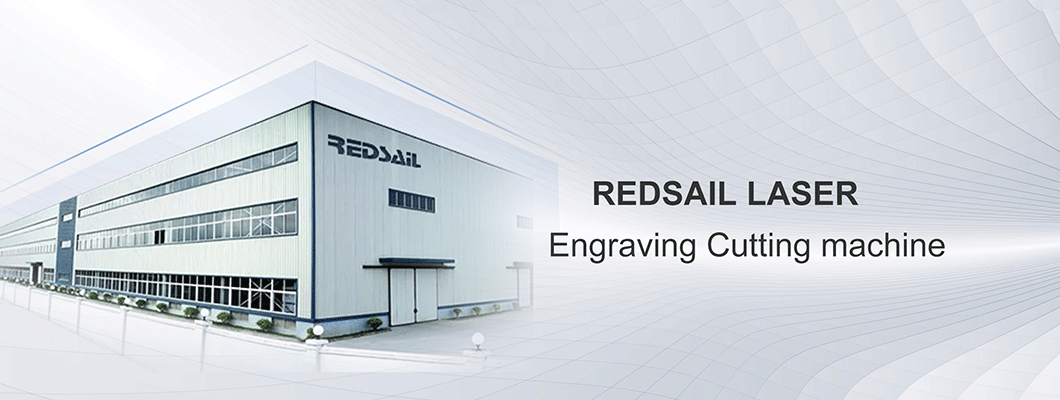
We all know that laser cutting machines transmit instructions from computers to machine tools to automatically perform a series of cutting tasks. Therefore, their advantages such as fast cutting speed and high cutting accuracy are incomparable to traditional cutting equipment. However, the types and structures of laser cutting machines vary, and the effects produced during processing may vary depending on the laser equipment. The main factors that affect the cutting quality and performance of laser cutting machines during the cutting process include laser beam quality, laser power, cutting speed, workpiece thickness, material type, etc.
Important factors affecting the efficiency of laser cutting machines:
1. Laser cutting machine power: If the laser power is too high or too low, it will directly affect the cutting quality. If the power is too high, it will lead to excessive melting of the cutting seam, and if the power is too low, the cutting speed cannot keep up with or even penetrate the metal plate.
2. Unstable computer system leads to slow cutting: prolonged operation of the equipment, CPU and hard disk heating, or defects in cutting control software, such as defects or cutting errors, can also delay cutting consumption and affect cutting quality.
3. Failure to save cutting process drawings and parameter settings: Previously used drawings and parameters were not saved in the computer. Hainan laser cutting machine operators can only rely on experience and eye observation. After manual operation of the laser cutting machine, automatic perforation and cutting cannot be achieved, and the efficiency of the laser cutting machine is naturally very low.
4. Inappropriate use of cutting method: When setting parameters, the cutting method used is too simple, with individual parts requiring perforation and intact cutting, without using cutting methods such as common edge, edge borrowing, and bridging. This leads to low cutting efficiency and severe waste of consumables.
Leave a Comment